We can discuss at length the unique properties of shell cordovan leather, why it is not technically considered leather from a scientific standpoint, and how its tanning process is lengthy and labor-intensive. However, first and foremost, we're talking about leather. That means, like any other leather, we need to tan and treat it with oils. This will be the focus of the text.
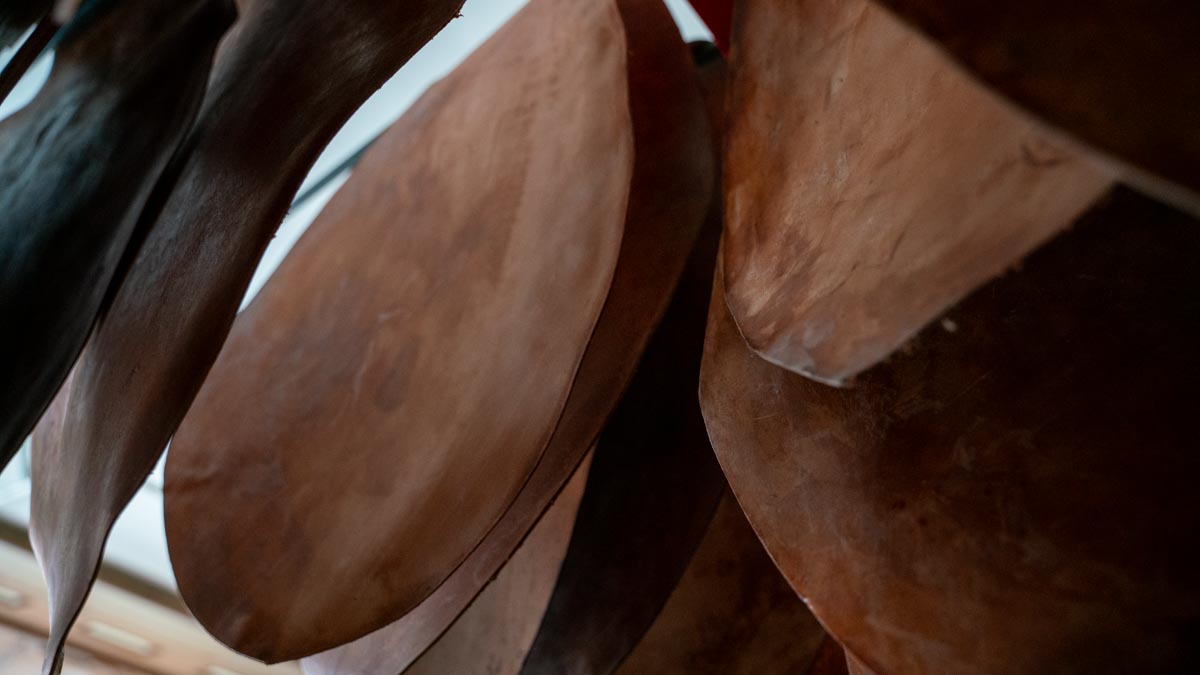
When I was preparing to write this text, I imagined the vast variety of materials used for tanning and greasing leather, and I was overwhelmed. I realized I couldn't possibly cover them even in ten articles like this one. But I decided to focus on why and what we use.
The answer to the first question is quite simple: we don't use materials that we couldn't either consume or apply to our own skin. Our product is alive, and it interacts with your skin every day. This means it shouldn't contain anything that could cause allergies or pose any level of risk to your health.

we don't use materials that we couldn't either consume or apply to our own skin
In the photo above, you can see six main materials that we use in production. From left to right, top to bottom, clockwise:
- animal fat
- oxidized oil
- bone oil
- vegetable oil
- natural tannins
- fat mixture
However, before moving on to describe each of them, I would like to outline the general process of shell cordovan production.
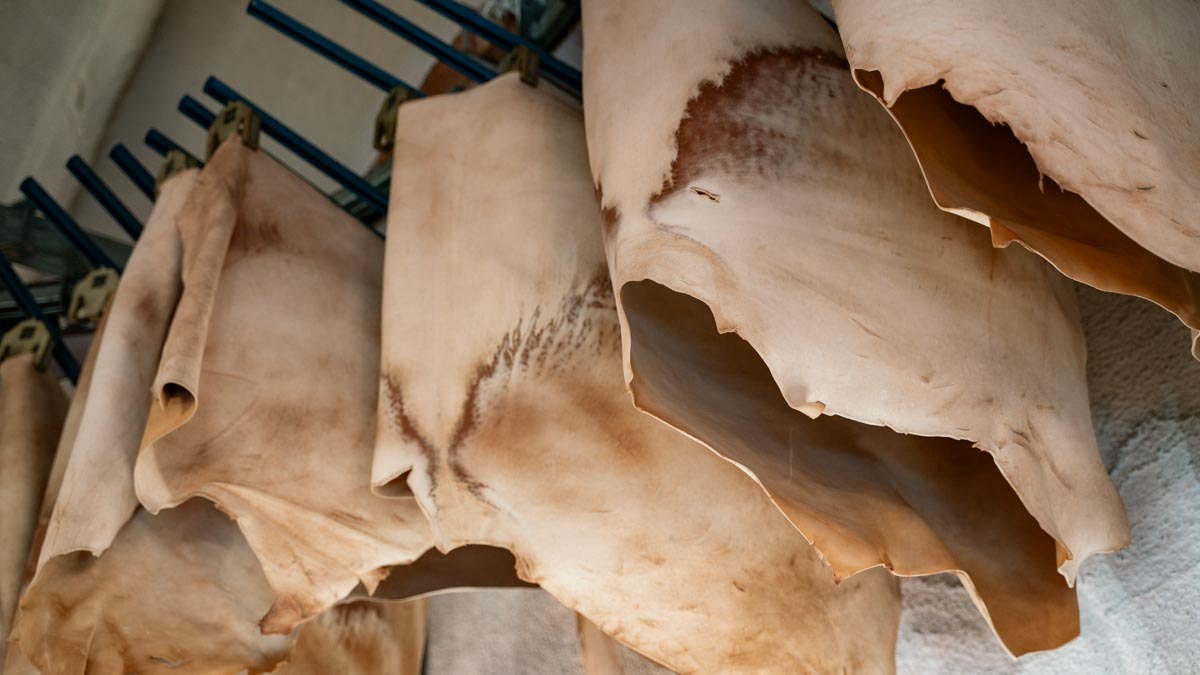
The main stages of shell cordovan production are as follows:
- Initial tanning of horse butts
- Splitting to working thickness
- Light shaving until the boundaries of the shell cordovan are clearly visible
- Cutting strips
- Initial rough shaving of shell cordovan, resulting in almost complete removal of material from the surface
- Re-tanning
- Greasing in a hot drum
- Straightening and drying
- Impregnation of leather with a mixture of oils and waxes
- Final finishing shaving
- Re-impregnation of leather with a finishing mixture of oils and waxes
- Dyeing and finishing
Thus, the very first ingredient we deal with is tannins. We only use natural tannins derived from plant extracts (barks, leaves, fruits) that are harmless to health and the environment. There are many synthetic tannins available to expedite and cheapen the process of tanning thick hides like horse butts quickly and evenly. However, we fundamentally refrain from using such auxiliary substances. We adhere strictly to natural ingredients without compromise.
In the photo below, you can see two of the tannins we use - quebracho extract and sumac.
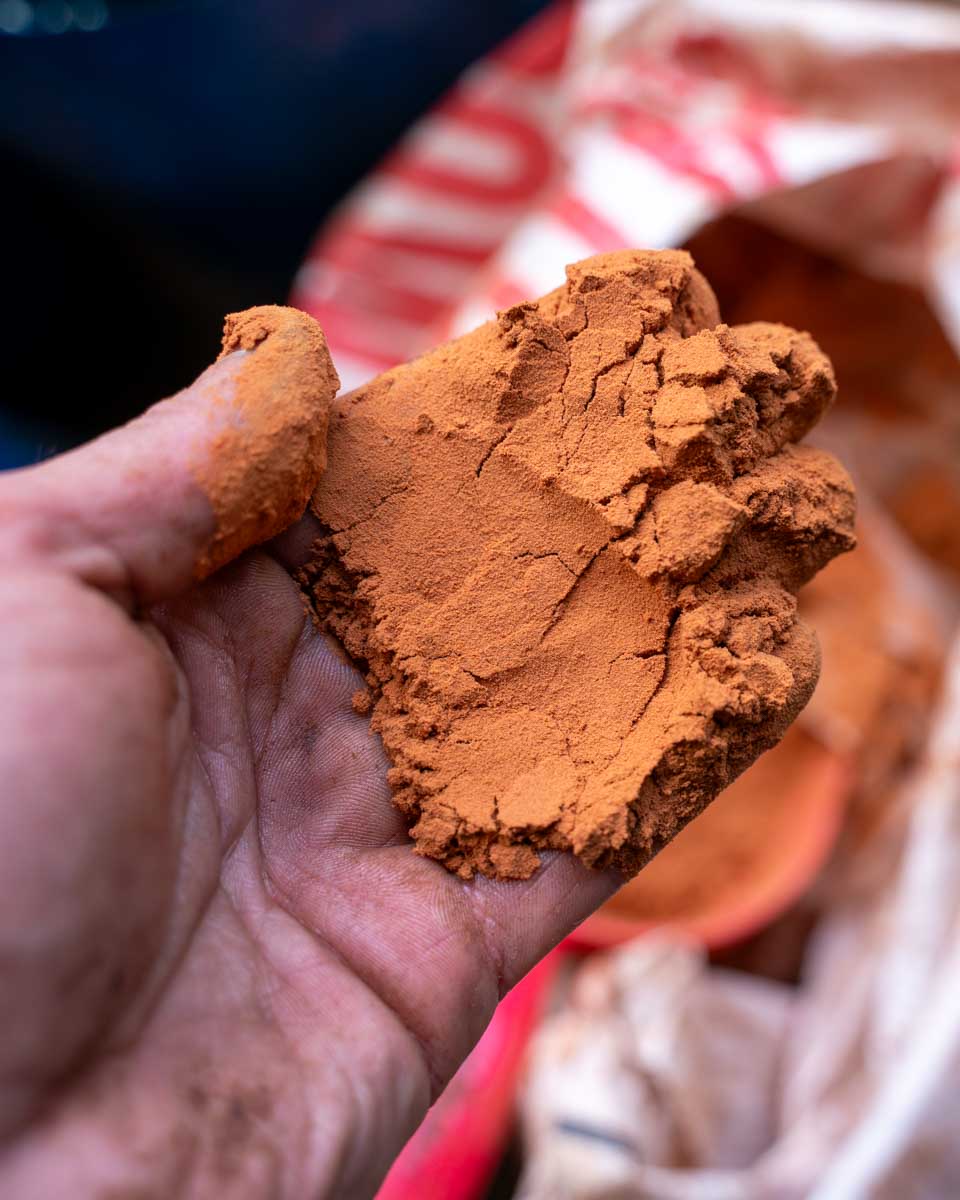
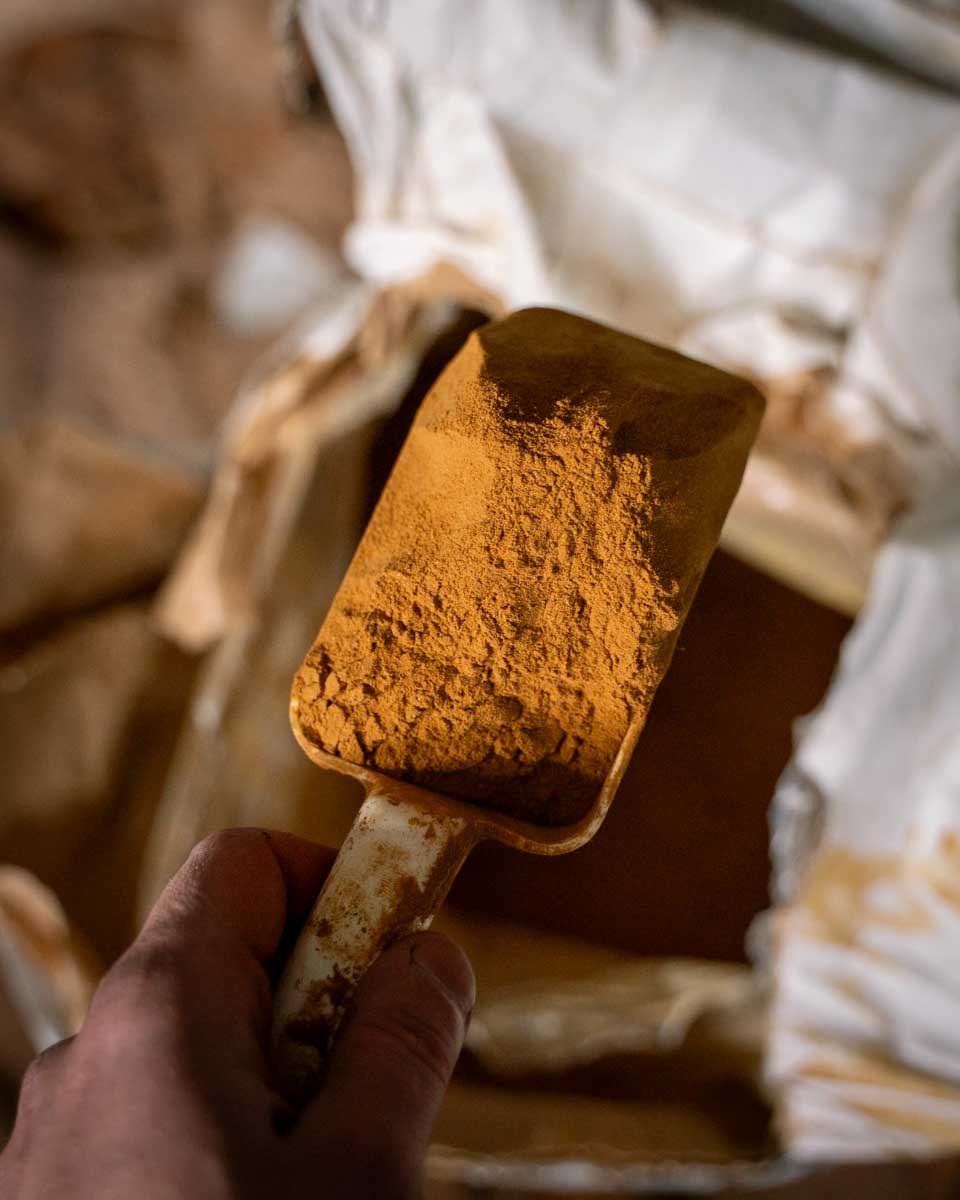
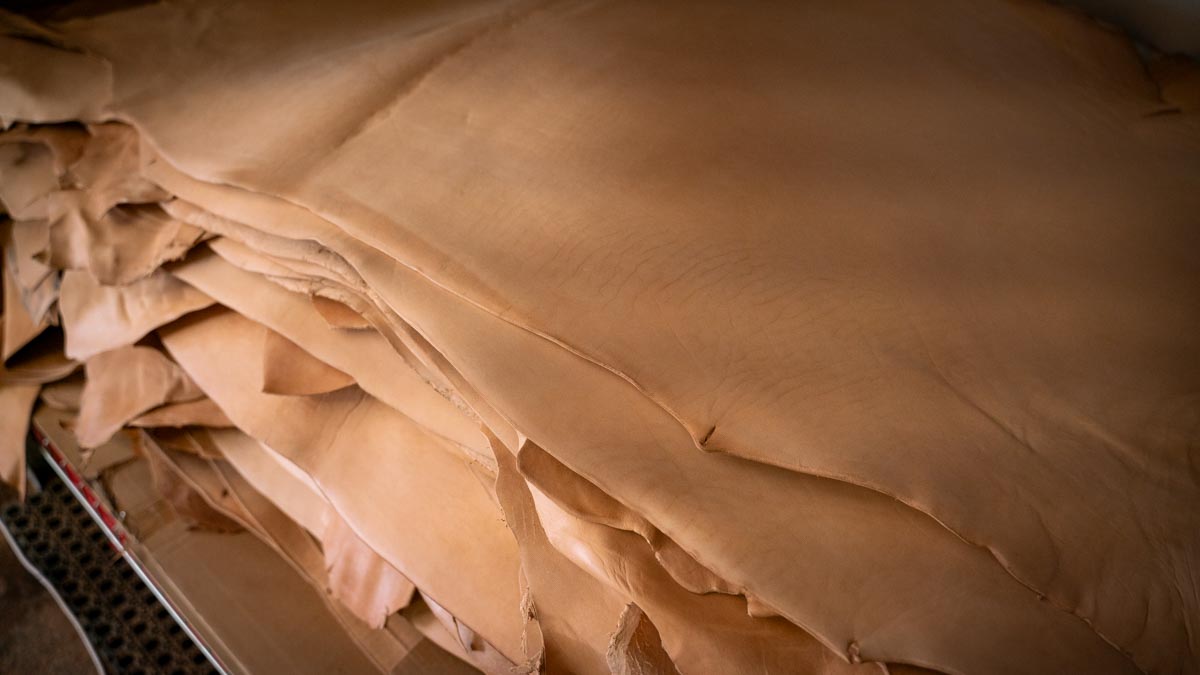
As a result of the first tanning process, we obtain a semi-finished product that already has the appearance and properties of leather, is stable, and ready for further processing (photo above). It's worth mentioning that tannins are rarely used individually but more commonly in a blend of several extracts, each with specific properties such as water solubility, tanning speed, acidity, and imparting various properties to the leather, such as density, strength, softness, color, and others.
Below, you can find information about tannins from books on leather production from the beginning of the last century.
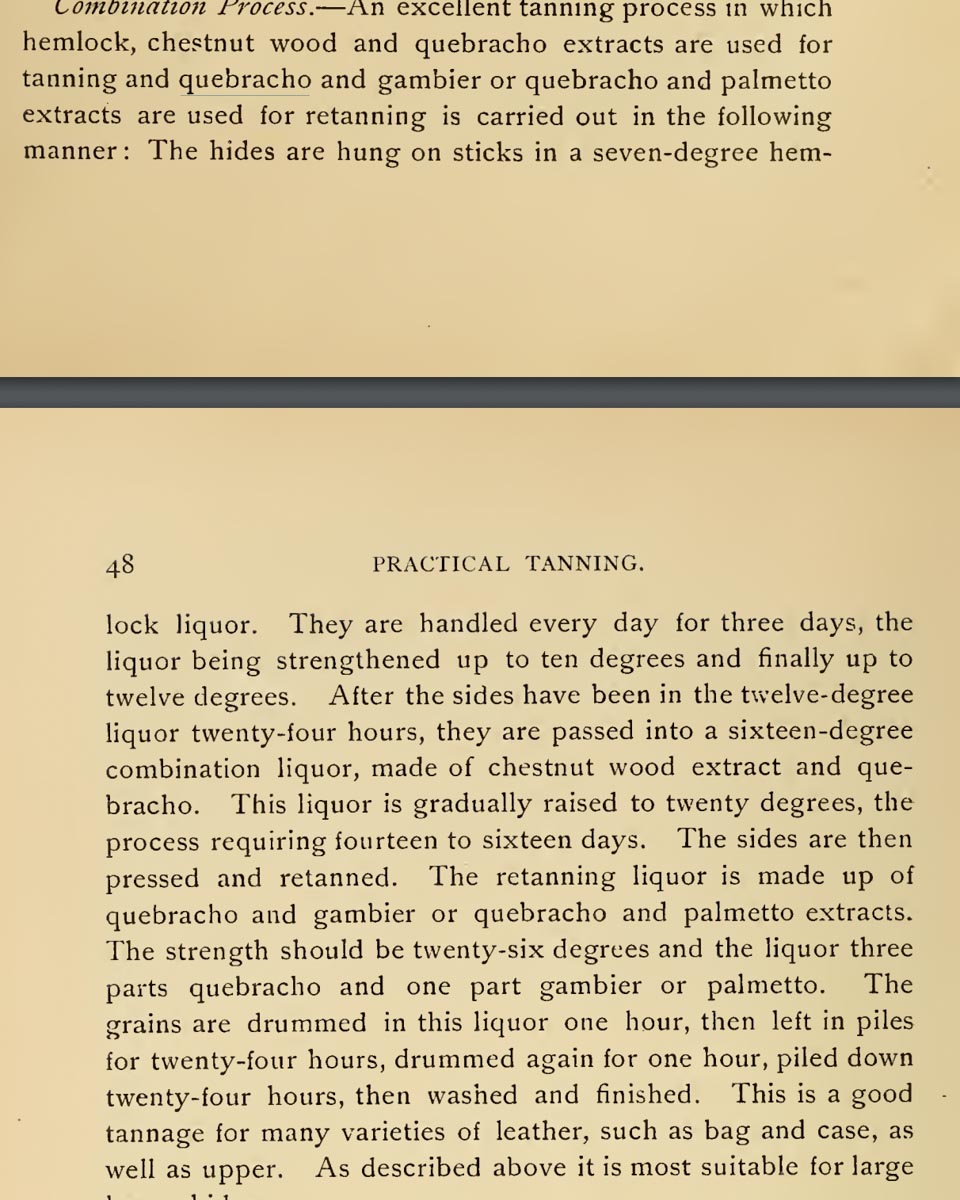
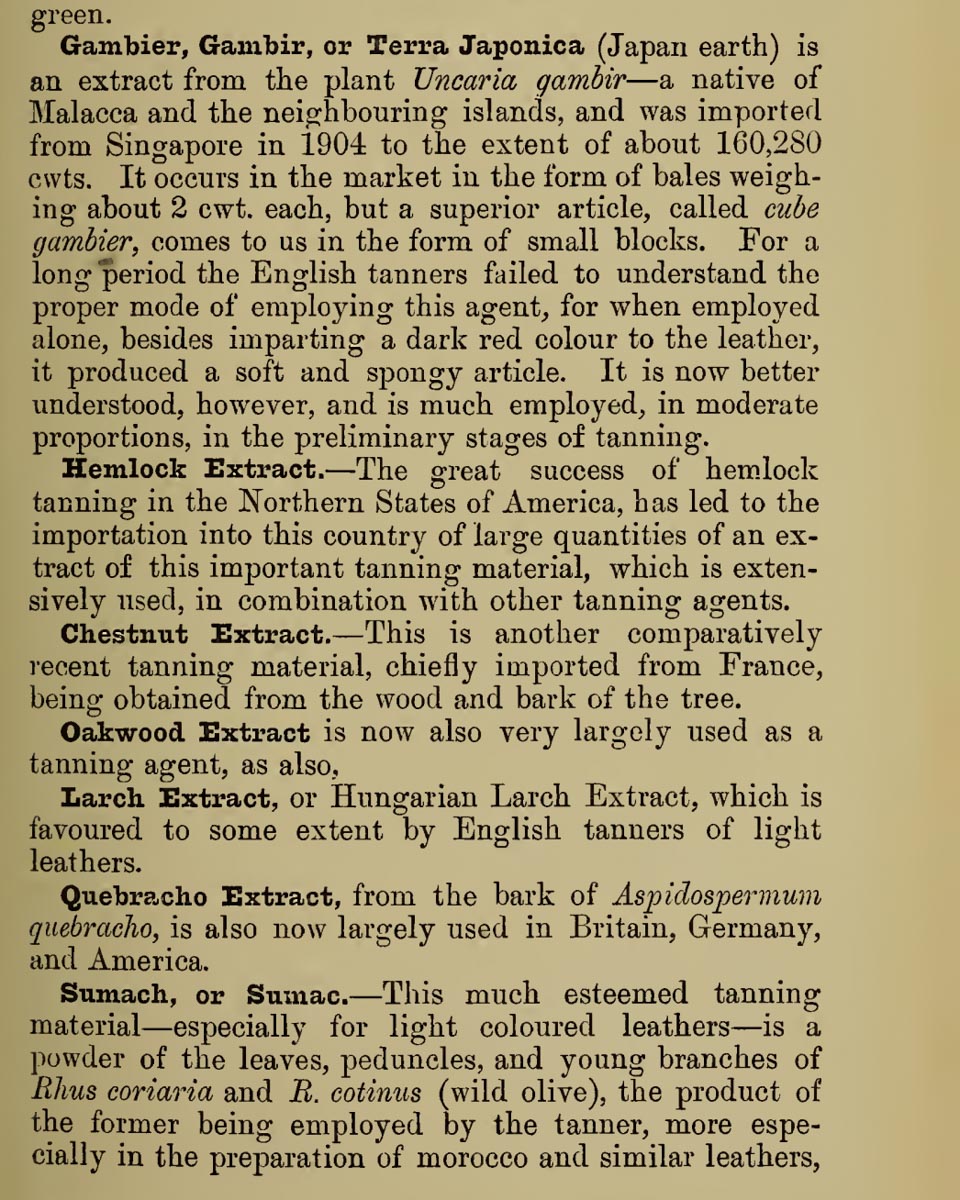
The next important ingredient is the fat mixture for hot greasing.
Each manufacturer has their own recipe for this mixture, developed over the years. In general, the purpose of this mixture is to impart essential properties to the leather, such as softness, flexibility, fullness, polishability, weather resistance, and others.
The main "classic" ingredients of this mixture are: foot oil, lard, fish oil, and waxes.
However, sometimes ingredients like lanolin, lecithin, proteins, whey, and others are used.
Our mixture is designed to be used in a hot drum with constant rotation.
Scroll through the slides to find out more details.
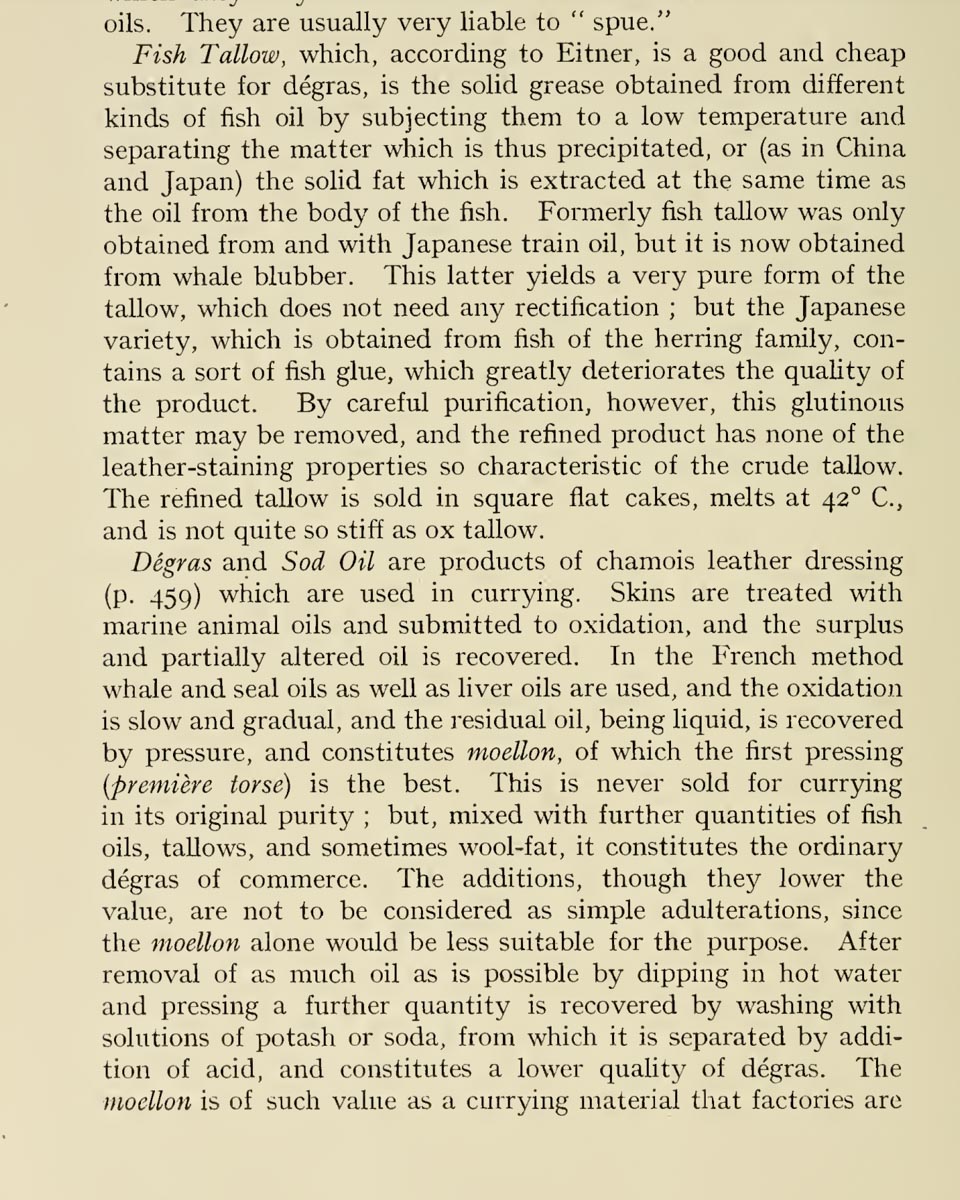
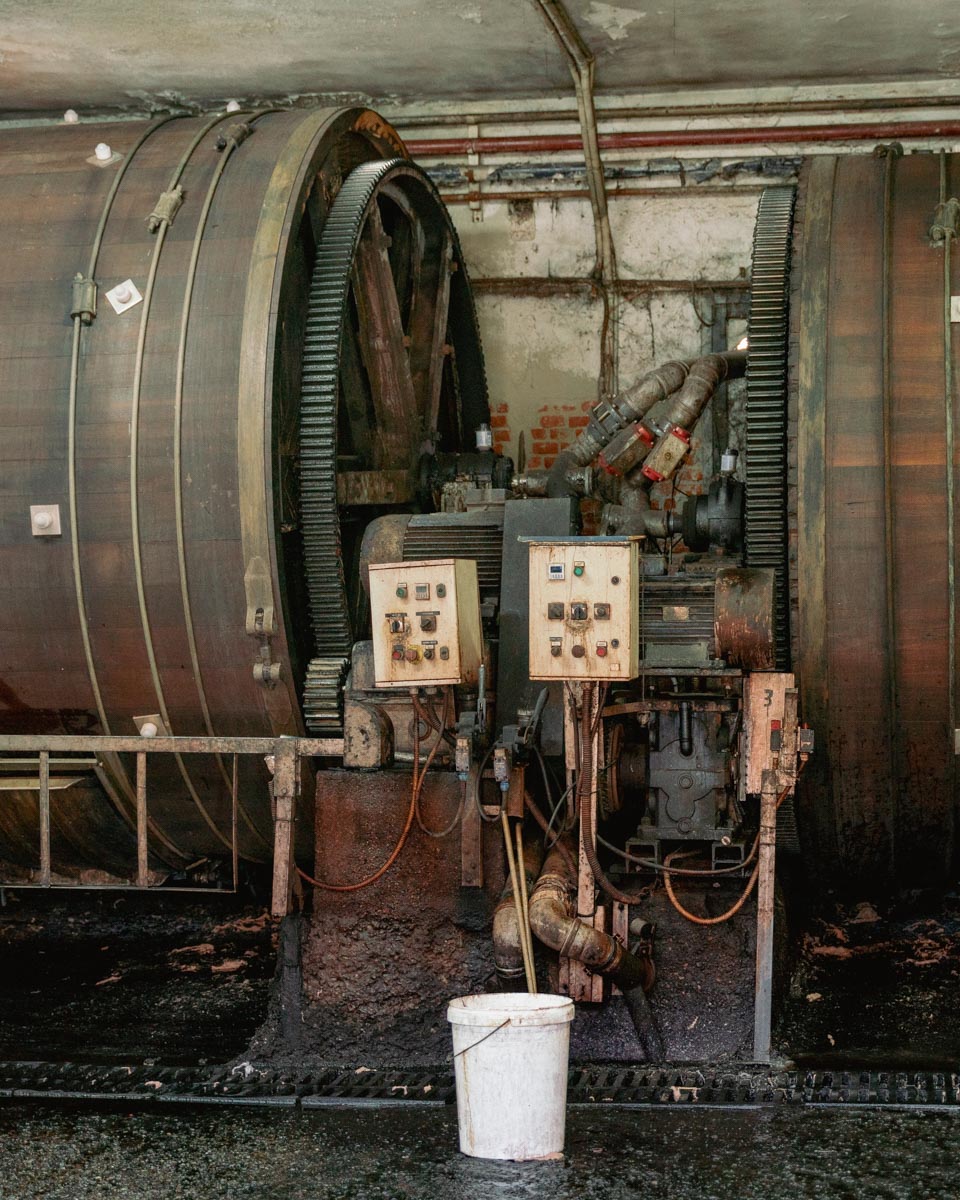
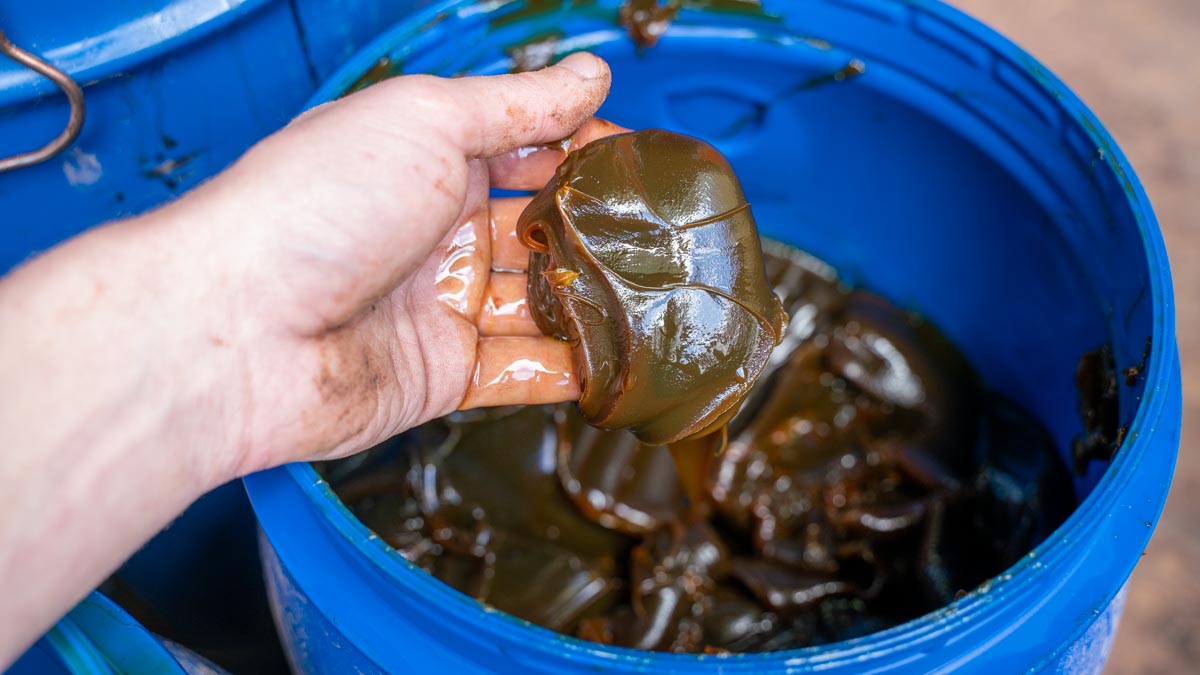
The last three ingredients worth mentioning are lanolin, foot oil, and oxidized fish oil.
We use them both in the "aging" process and for finishing.
However, there is a difference in their combinations and proportions. Without revealing too many details, it can be said that at the finishing stage, another oil - vegetable oil - is added to the mixture. It was in the white canister in the first photo.
Here are a few words about each ingredient:
1. Lanolin: Lanolin is a natural wax obtained from sheep's wool. It is used for its emollient properties, helping to soften and moisturize the leather.
2. Foot oil: foot oil is derived from animal hooves and is rich in nutrients that nourish and condition the leather, enhancing its flexibility and durability.
3. Oxidized fish oil: Oxidized fish oil is fish oil that has undergone oxidation, resulting in changes to its chemical composition. It is often used in leather finishing to provide water resistance and suppleness to the leather.
At both stages, the oil mixture is applied in a warm state using a brush (as seen in the photo above). Afterward, we let the leather "age" for a period of up to 30 days. This allows the oils to evenly distribute within the leather and acquire the appearance and properties we desire.
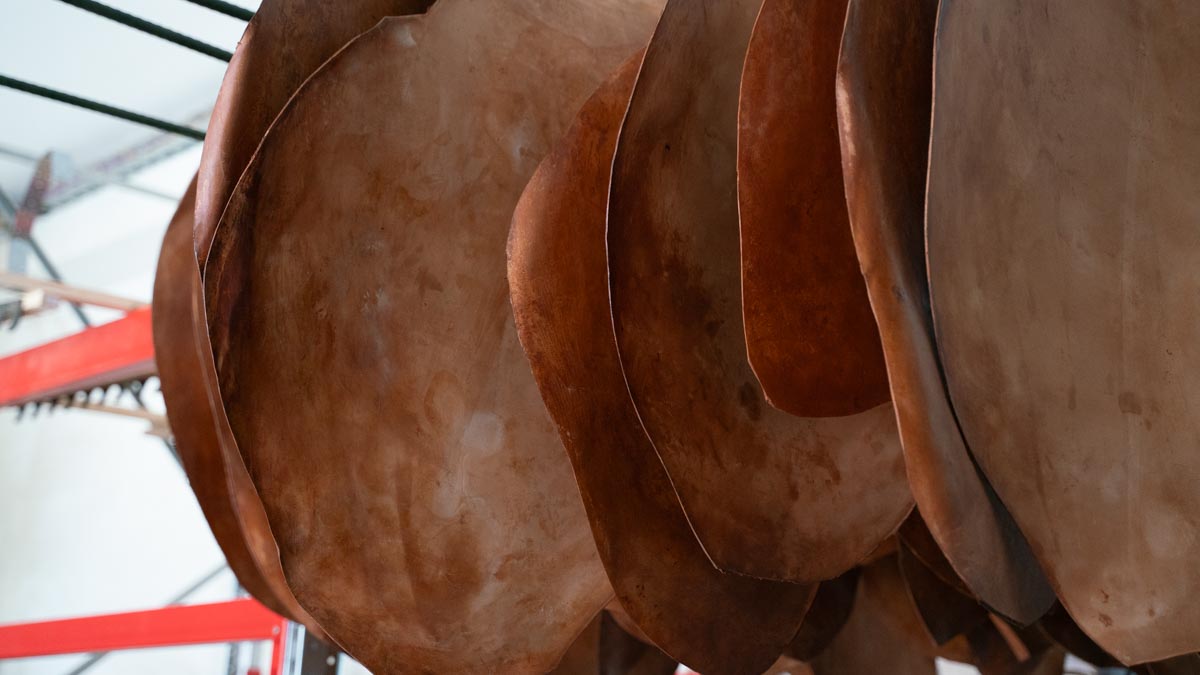
We've aimed to write this text informatively and without sensitive details for our business. We hope you found this article informative.
In conclusion, we reiterate that we only use the simplest, natural, and harmless ingredients that have stood the test of time.
Below, you'll find several photos from leather production dating back 100-150 years. We adhere to the materials and technologies people used at that time and thank you for sharing our commitment to reviving time-tested traditions.
.jpg)
.jpg)
June 1st, 2024
Maxim Bobrikov